Mitä on laatu?
Laatu mielletään arkisessa ajattelussa normaalituotetta hieman kalliimmaksi tuotteeksi, joka on jonkun tunnetun brändin tuottama. Työympäristössä laatu mielletään taas usein nykypäivän laatujärjestelmien [1] vaatimuksien täyttämiseksi. Nämä edellä mainitut ajatukset ovat niin syvällä meidän jokaisen mielessä, että tämän johdosta laatu ja laadunparannus mielletään aina ylimääräiseksi kuluksi. Miten itse suhtaudut väitteeseen, että laadun parantaminen laskee hintaa? Niinpä, pidät väitettä epäuskottavana ja mahdottomana. Pyydän sinua lukemaan tämän artikkelin loppuun ja pohditaan kysymystä sen jälkeen uudelleen.
Vaikka yritys tuottaisi todella laadukkaita tuotteita ja olisi hyvin menestyvä, löytyy prosesseissa aina kehitettävää parempaan suuntaan. Prosessin kehityksellä ei tarkoiteta töiden lisäämistä prosessiin, vaan töiden sujuvoittamista. Nykyaikana kaikkien organisaatioiden ja prosessien tulee kehittyä jatkuvasti ympärillä kehittyvän maailman mukana, jos yritys haluaa pysyä kilpailukykyisenä nykyisessä tiukassa globaalissa kilpailussa.
Ensimmäinen ja tärkein askel on tunnistaa ja tunnustaa, että yrityksen toimintamalleissa ja tavoissa on ongelmia. Tämän jälkeen tuleekin todella haastava vaihe. Miten nostetaan ongelmat esille niin, että työntekijät eivät koe ongelmien selvitystä syyllisien etsimiseksi, vaan kehittämiseksi. Muutamia tällaisia kehitysprojekteja seuranneina voin todeta, että ensimmäiseen tiedotustilaisuuteen kannattaa panostaa paljon. Ihmisten innostuessaan heti alkuun projektista he ovat aktiivisesti mukana ja suhtautuvat muutoksiin positiivisesti. Jos ensimmäisessä tiedotustilaisuudessa asia ymmärretään väärin ja projekti saa työntekijät varuilleen tai epäileviksi, on projektin edistäminen ja loppuun saattaminen todella haastavaa. Ihmiset pitää saada innostumaan ja kiinnostumaan virheistä ja etenkin oman työn kehittämisestä.
Nykyaikaisessa digitalisaation maailmassa on mahdollista rakentaa todella laajoja ja tarkkoja raportointi työkaluja, joilla ongelmien määriä ja kategorioita on helppo seurata. Ennen näitä tulee olla käytössä työkalut, joilla ongelmien raportointi on helppoa, joka puolestaan johtaa siihen, että pienistäkin ongelmista raportoidaan pienellä kynnyksellä. VEO Oy:llä tähän on keksitty todella hyvä toimintamalli. Kaikilla tuotannon työntekijöillä on käytössään mobiilipäätelaite ja siinä mobiili applikaatio, jolla työntekijä tekee tunti- ja materiaalikirjaukset. Applikaatioon on lisätty yrityksen toiveesta poikkeamien kirjaus mahdollisuus. Työntekijän havaitessa puutteen tai ongelman työssään, hän tekee applikaatiolla siitä poikkeaman. Poikkeama ohjautuu suoraan oikeille henkilöille, koska järjestelmä tietää mitä työtä työntekijä tekee. Tämän järjestelmän kautta voi tehdä myös kehitysehdotuksia.
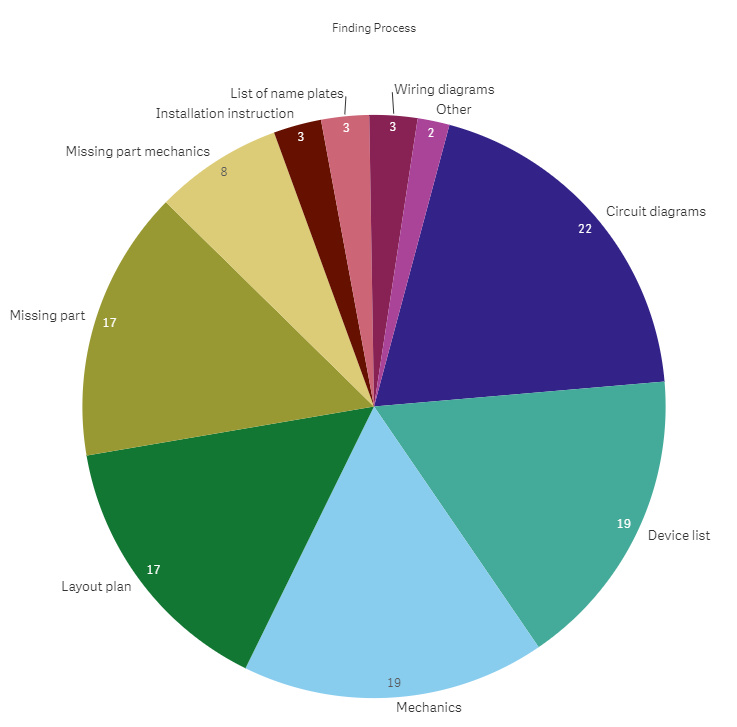
Kuvassa VEOn sisäisen raportointityökalun näkymä suunnitteluun kirjatuista poikkeamista. Ympyrä on jaettu alikategorioittain ja siitä on helppo havaita, minkä osa-alueen kehittämiseen kannattaa kiinnittää huomiota.
Kun laadun parannus hanke aloitetaan, tulee yrityksessä ensimmäisenä selvittää mitkä osa-alueet aiheuttavat eniten ongelmia. Tämän jälkeen arvioidaan ongelmien taloudellisia vaikutuksia. Edellä olevien toimenpiteiden jälkeen priorisoidaan kehityshankkeet. Priorisointia tehdessä yleinen ajatus on se, että aina tulee ensimmäisenä paneutua siihen, josta on suurinta taloudellista haittaa. Asia ei ole mielestämme ihan näin mustavalkoinen. Ongelmat tulee kyllä järjestellä arvioitujen taloudellisten vaikutusten mukaan. Tämän järjestelyn jälkeen tulee pohtia ongelmien ratkaisujen kustannukset. Ongelman ratkaisun tulee aina säästää enemmän rahaa, kuin sen ratkaisu vie, ellei kyse ole lain tai asetuksen vaatimusten täyttämisestä. Lyhyesti tiivistettynä 10 000€ kulua vuodessa aiheuttavaa ongelmaa ei kannata korjata käyttäen 15 000€ vuodessa. Ongelmat, jotka ovat nopeasti ja kustannustehokkaasti ratkaistavissa, ratkaistaan ensimmäisenä [2]. Pareton periaate tukee tätä ajatusta. Pareto-analyysin mukaan, missä tahansa ilmiössä 80 % seurauksista johtuu 20 %:sta syistä. [2] Nopeat toimenpiteet luovat myös positiivista kehitysilmapiiriä, koska henkilöstö näkee konkreettisia muutoksia, eikä vain hienoja suunnitelmia. Tämä innostuminen saa aikaan kehityshenkistä ilmapiiriä ja hankalemmatkin ongelmat saavat useammasta suunnasta ratkaisuehdotuksia.
Ongelmien tutkiminen ja juurisyiden etsintä
On tärkeää rajata hyvin alkuvaiheessa tutkittavien ongelmien määrä, jottei valita isoa määrä erilaisia ongelmia ja tutkia kaikkia vähän, mutta ei ratkaista mitään2. Tämän takia opinnäytetyössä [3], jossa käsiteltiin tuotannon tehostamista projektityyppisessä tuotantoympäristössä, rajattiin ongelmien tyypit heti alkuun neljään suurimpaan ongelmia aiheuttavaan tekijään: suunnitteluvirheet, materiaalista johtuvat ongelmat, asennustekniset virheet ja aikataulutekniset virheet.
Ongelmia tutkittaessa suurin virhe on tukeutua vain yhteen tietolähteeseen. Klassinen sanonta: tilastosta saadaan juuri sellainen, kun halutaan johtaa helposti harhaan. Tilastoivat raportointityökalut ovat hyviä työkaluja, mutta niiden toimintalogiikka tulee tuntea hyvin, jotta tuloksia osataan tulkita oikein ja tarvittaessa kriittisesti. Haastattelut ovat myös loistava tiedonlähde. Haastateltavien henkilöiden tulee olla eri työtehtävissä olevia henkilöitä, jotta ongelmista ei saada yksipuolista kuvaa. Vielä nykyaikanakin osa tiedoista on vain fyysisinä dokumentteina tai sähköposteissa. Tämä vaatii tutkivalta henkilöltä suurta työmäärää, mutta tämäkin työ on tehtävä. Sieltä saattaa tutkija, joka katsoo asiaa täysin ulkopuolisin silmin ilman ennakkoajatuksia, havaita ongelmia, joista kukaan ei ole maininnut haastatteluissa tai ei ole tilastoitu mitenkään [4].
Ongelmia tutkivan ryhmän tai työntekijän tulee omata laajasti tietoa tuotteen koko matkasta suunnittelusta valmistukseen ja valmistuksesta toimitukseen. Vain näin ongelmien ratkaisuja pohditaan koko yrityksen kannalta taloudellisemmalla tavalla.
Miksi tällainen kehityshanke kannattaa?
Projektityyppisessä tuotannossa laadukas suunnittelu, hyvin toimiva materiaalienhankintaketju ja hyvin suunniteltu projekti aikataulu minimoi tuotteen tekemisen aikaiset pysähdykset. [5] Työn keskeytyessä hukataan aina tehokasta tuotanto aikaa. Ongelmasta riippuen yksi virhe saattaa “polttaa” 15-minuutista useisiin tunteihin tehokasta tuotanto aikaa. Lisäksi tämä pitkittää projektin valmistumista, mikä taas aiheuttaa lisää aikataulullisia ongelmia ja pysähtynyt projekti sitoo tuotantotilaa, joka voisi olla tehokkaassa käytössä. [6] Mitä enemmän asennusteknisiä virheitä on, sitä enemmän kuluu työaikaa tehdastarkastukseen ja virheiden korjaamiseen. Eli kun panostetaan laadukkaaseen suunnitteluun ja asennustyöhön vältetään turhat työnpysähdykset [7]. Materiaalihankinta prosessin ja aikataulun laadinta prosessin jatkuva parantaminen mahdollistaa tuotannon resurssien ja tilan tarkemman määrittelyn.
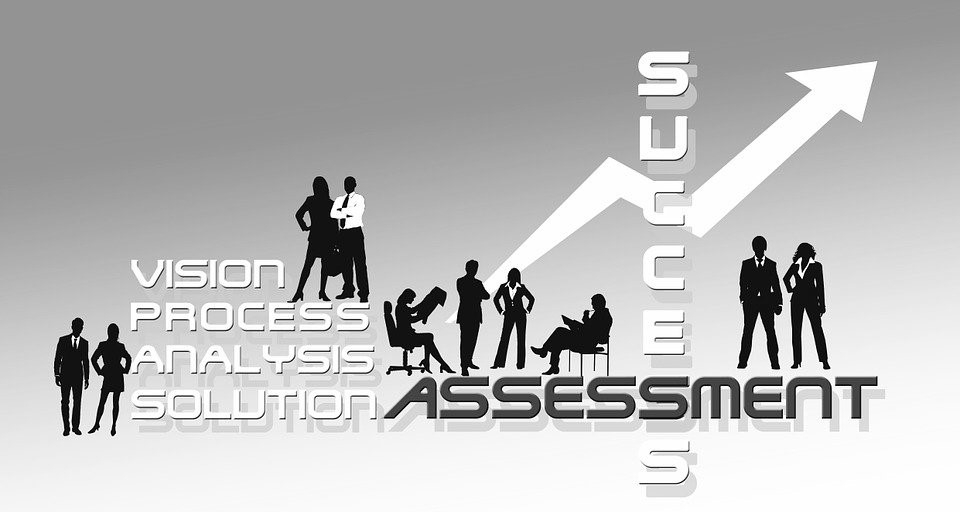
Laadun ja tehokkuuden ollessa hyvällä tasolla se vaikutta myös tuotteiden läpimenoaikoihin. Yritykset, jotka tilaavat isoja ja arvokkaita projekteja, haluavat sitouttaa pääomaansa mahdollisimman vähän aikaa ja näin ollen nopeat läpimenoajat ovat kilpailuetu. Kansan omaisena esimerkkinä voitte miettiä seuraavaa: jos käyt kahdessa eri autokaupassa katsomassa ominaisuuksiltaan kahta hyvin saman tyyppistä autoa, jotka ovat samanhintaisia, mutta toisen saat kuukauden päästä ja toisen puolen vuoden päästä niin kumman valitset?
Laadun parantamiseen liittyvät ratkaisuehdotukset jakautuvat neljään ryhmään
- Suunnittelun kehittäminen
- Materiaalihankinnan kehittäminen
- Asennustekninen kehittäminen
- Aikataulutekninen kehittäminen
Opinnäytetyössä tutkittiin pienjännitekojeistojen tuotannon tehostamista laadukkaiden toimintatapojen kautta [3] Opinnäytetyössä löydettiin useita kehityskohteita ja tapoja, jotka sopivat varmasti myös muidenkin alojen tuotantoon, mutta parhaiten projektityyppiseen tuotantoon, jossa ei tuoteta sarjatuotantona massatavaraa isoilla volyymeillä.
Yrityksen koosta riippumatta on sähkösuunnittelussa varmasti käytössä nykyaikaiset ohjelmistot, joissa on laajat suunnitteluohjelmien automaattitarkastukset. Niiden käyttö tulee viedä niin pitkälle kuin mahdollista. Pitää myös muistaa, että hienot ohjelmat ja ominaisuudet ovat turhaa, jos niitä ei osata käyttää. On varmistettava, että yrityksen henkilöstö osaa käyttää niitä ja tarpeen vaatiessa järjestää koulutusta ohjelmiston käyttöön. Suunnittelutyössä kannattaa hyödyntää tarkastuslistoja, jotka ovat nykyajan digitalisaation maailmassa helposti toteutettavissa. Suunnittelun on tuotettava valmistusdokumentaatio, josta löytyy kaikki tarpeellinen tieto tuotannolle. Ei lisätietoja esimerkiksi sähköpostilla tai suusanallisesti. Kaiken tiedon on löydyttävä yhdestä paikasta ja oltava kaikkien tiedossa.
Materiaalit, joilla on pitkät toimitusajat, tulee olla omalla pitkän toimitusajan komponenttien listalla, jotta ne osataan tilata muita tilauksia aikaisemmin ja ne määritellään heti suunnittelun alkuvaiheessa toiminnanohjausjärjestelmään. Listaa on myös päivitettävä koko ajan materiaalisaatavuuden mukaan. Toiminnanohjausjärjestelmä ohjaa oikean materiaalin oikealle projektille oikeaan aikaan [5]. Tässäkin tulee huomioida käyttäjien riittävä osaaminen järjestelmän käyttöön.
Asennustekninen kehittäminen virheiden vähentämiseksi: Koulutus ja prosessien muutos, mitä tehdään missäkin vaiheessa ja selkeät rajat mikä kuuluu minkäkin työvaiheen vastuualueeseen. Asentajien tulee olla tietoisia, mitkä ovat yleisimmät virheet niin he tietävät kiinnittää huomiota erityisesti niihin työvaiheisiin, missä virheitä esiintyy. Asentajien tietoisuutta virheiden vaikutuksesta tuotannon kannattavuuteen on myös lisättävä.
Aikataulutekninen kehittäminen projekti tyyppisessä tuotannossa on haastavampaa kuin sarjatuotannossa, mutta on ehdoton edellytys kannattavalle liiketoiminnalle. Projektien aikataulujen ja tuntimäärien tulee olla realistisia, mutta ei kuitenkaan ”liian varman päälle” laskettuja ettei menetetä kilpailukykyä tästä syystä. Hyvin suunniteltu aikataulu on myös tehokkuuden kannalta hyvä. Liika kiire ajaa projektin yliresursointiin ja työtuntien kasvuun, liian löysä aikataulu taas sitoo tuotantotilaa ja materiaalin hankintaan käytettyä pääomaa [5]
Toivon että miellät nyt muutaman minuutin lukemisen jälkeen laadun erilaiseksi, kuin mitä pohdit sen olevan vielä hetki sitten. Laatu ei ole pelkkää hifistelyä ja kalliita materiaaleja. Laatu voi olla myös sujuvaa tekemistä ja hyvin toimivia prosesseja, joka taas johtaa laadukkaaseen kokonaisuuteen. Tekemisen ollessa laadukasta, ei tehdä mitään turhaan. Aika mikä on hukattu ennen epäoleelliseen tekemiseen ja virheiden korjaamiseen voidaan jatkossa käyttää tuottavaan työhön ja myös virheellisen tuotteen päätyminen asiakkaalle on epätodennäköisempää.
Kaiken onnistuessa laadun parantuminen saattaakin alentaa tuotetun tuotteen hintaa. Siinä onkin sitten myyjänkin huomattavasti helpompi lähteä hakemaan uusia asiakkuuksia, kun kykenee myymään laadukkaampaa tuotetta edullisempaan hintaan kuin kilpailijat. Toistan saman kysymyksen, minkä esitin artikkelin alussa ja toivon, että olet itsellesi rehellinen vastatessasi kysymykseen: Miten itse suhtaudut väitteeseeni, että laadun parantaminen laskee hintaa? Niinpä. Siinä jokaiselle mietittävää millä tavoin tahtoo itse toimia tai millä tavoin toimivassa yrityksessä haluaa työskennellä.