I won’t delve into the details of sourcing used cooking oil. This could come from your own kitchen, friends who own a deep fryer, or acquaintances in the restaurant industry. Many people with deep fryers are often happy to give away their used oil, as it saves them the hassle of taking it to a recycling centre.
The first step, and perhaps the most tedious, is filtering the used oil. Start with larger filters (500, 200, and 100 microns). This initial filtration is sufficient for removing larger impurities; finer particles will either be removed during the glycerin separation or filtered out later. While you could do a more thorough filtration now, the high viscosity of the oil makes it a slow process. Heating the oil can help, but it’s still time-consuming.
To convert the oil into biodiesel, you’ll need two main components: an alcohol and a catalyst. Methanol (CH₃OH) is the preferred alcohol and is widely available in bulk from wholesale suppliers. Alternatively, you can produce methanol yourself through methods like the dry distillation of deciduous wood. You’ll need about 20% of the total weight of the entire mixture (oil, methanol, and catalyst) in methanol. Adding more is ok: excess methanol can be recovered and doesn’t hurt the reaction; it makes sure the reaction fully completes and no oil remains.
For the catalyst, use either Potassium Hydroxide (KOH) or Sodium Hydroxide (NaOH). Potassium Hydroxide is commonly available and can even be made from hardwood ash (lye). You’ll need roughly 1% of the total weight of the entire mixture in catalyst, but adding more is no issue as it can be recovered at the end.
A word of caution: these chemicals require careful handling. Methanol is toxic and should not be inhaled, ingested, or allowed to come into contact with the skin. Potassium hydroxide powder should only be handled with proper protective equipment, including a mask, and contact with eyes or skin must be strictly avoided. Wear gloves, safety glasses and respirator – and work outdoors when possible.
Let’s examine the chemical reaction, the resulting products, and the conditions required for optimal yield. For this discussion, we’ll assume rapeseed oil as the base. While other oils may require slight adjustments to temperature and reaction time, the parameters outlined here should still produce satisfactory results in most cases.
Step one in the process is to dissolve the potassium hydroxide in the methanol. This creates potassium methoxide. Now typically, you would think the reaction looks like this:
KOH + CH3OH → CH3OK + H2O
However, the reaction between potassium hydroxide (KOH) and methanol (CH₃OH) involves ionic dissociation because KOH is a strong base and ionizes in methanol. The reaction produces potassium ions (K+) and methoxide ions (CH3O–), without forming water as in aqueous reactions. This means the complete ionic reaction looks like this:
KOH + CH3OH → CH3O– + K+ + H+
In the second step of the process, potassium methoxide is added to the oil, initiating the transesterification reaction. To better understand this reaction, let’s first examine the structure of oil at the molecular level. Oil is a triglyceride (or triacylglycerol), a molecule composed of a glycerol backbone bound to three fatty acid chains. This is shown in the image below.
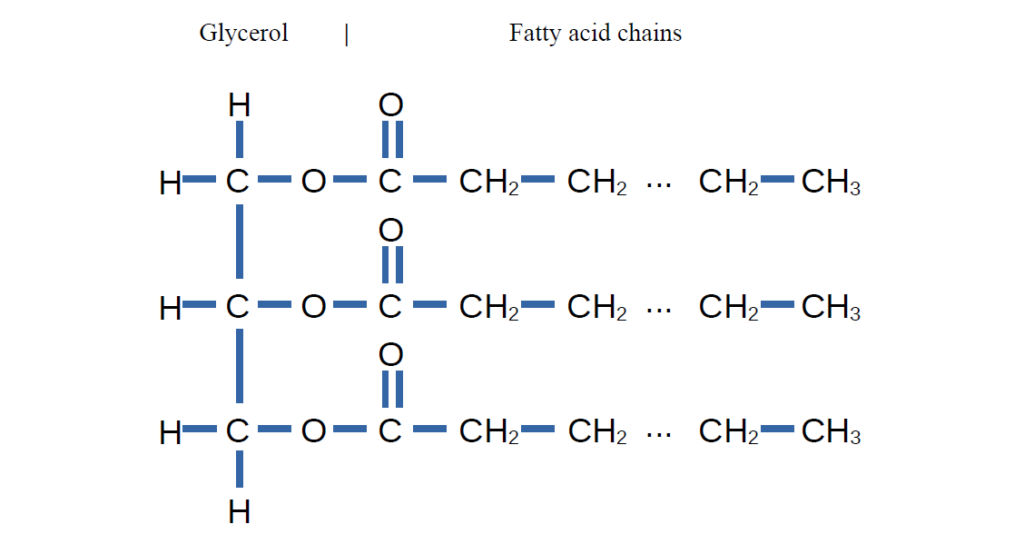
In the reaction with oil, the potassium methoxide attacks the carbonyl group of the triglyceride. This creates an unstable tertiary intermediate, which quickly rearranges and collapses, releasing a methyl ester of the first fatty acid. This is shown in the image below, where R1 represents the first fatty acid chain.
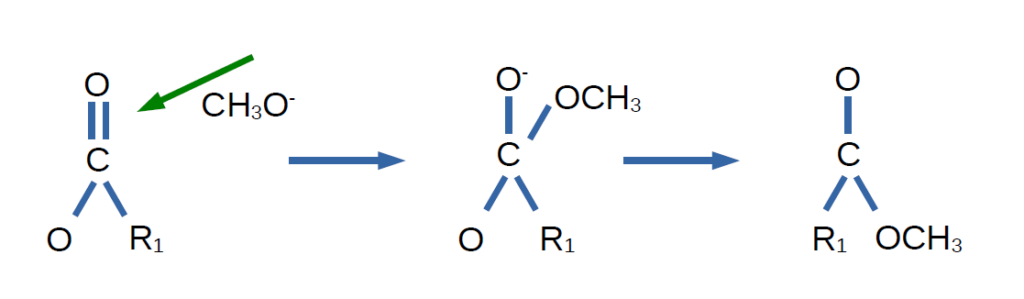
Then, the glycerol backbone is protonated by a water molecule (usually produced by side reactions). The hydroxide ion (OH⁻) remains in the solution and participates in the reaction, allowing the catalyst to continue facilitating the esterification. This is why KOH is called the esterification catalyst, and it can be recovered at the end of the process for reuse in the next batch. This process repeats until all three fatty acids are converted into their respective methyl esters, leaving the glycerol backbone free as glycerin. Overall, the chemical process looks like this:
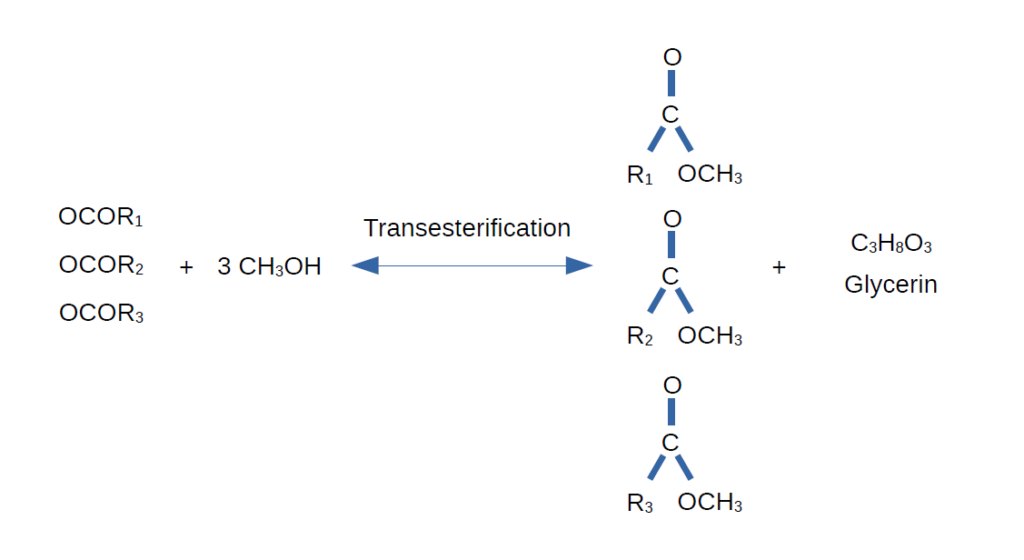
For optimal results, the mixture should be heated to 90°C and stirred with an agitator for 45 minutes. These parameters are based on a study published in 2024 [1], which helped improve my existing process. According to the paper, this approach should yield approximately 89%. While the exact yield of my most recent batch is unknown, it was higher than that of previous batches.
Once the reaction is complete, let the mixture settle overnight. The dense glycerin will settle at the bottom, while the biodiesel will remain on top. You can then decant or pump the biodiesel from the top layer.
Next, wash the biodiesel by pouring water over it, mixing well, and allowing it to settle. The biodiesel will float on top of the water. If the vessel is set up for it, you can remove the water from the bottom. Repeat this process until the water that’s removed is clear, indicating that any remaining soap or unreacted hydroxide has been flushed out. You can now pass the biodiesel through a one micron filter if needed to remove any remaining particulate matter that was in the oil.
Finally, to remove any remaining water, you can either boil the biodiesel or use a drying agent such as sodium sulfate (Na₂SO₄) or molecular sieves. Let it sit overnight, then pour out the now-dry biodiesel. This step is optional for many applications.
The glycerin and water from washing can be processed to recover excess methanol through distillation. After the methanol is removed, the KOH catalyst can be recovered, as it will settle out as a solid. The remaining glycerin can be processed further to make soap after removing any impurities left from the oil. If not, it can simply be composted.